NBC
Series Carbon Dioxide Protection Welding Machine
|
Because of carbon
dioxide's acting as protective medium, this series of welding
machine is a nationally promoted energy-saving
product. It can butt weld part of low-carbon steel,
low-alloy steel and fillet weld. This series apply to
welding thin plate materials and has such advantages
as high efficiency and little deforming after welding.
|
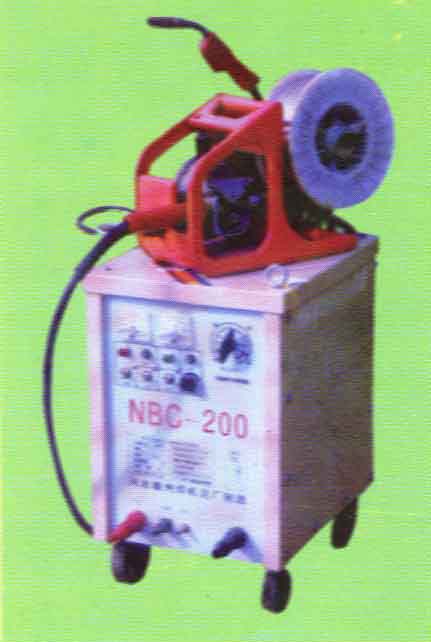
|
The
use of notes
1. Features
SCR
welder function and performance beyond the ordinary
1) No remote control cables and improve mobility, reduce the
dropping of trouble.
2) The design, welding dust has been considerably improved, and
applied to a wide range of fields and space.
3) have current, voltage adjustment / simple command
transformation, both beginners and skilled individuals, and have
handy.
2.Attention
to safety issues
To
ensure safe operation, must please observe the following :
Avoid
personal accident occurred warning
1) Grounding attention welder
To
prevent electrocution, electrical professionals in accordance
with legal standards implemented by the grounding.
2)Clothes
to wear protective equipment safety
To
prevent eye irritation and skin burns, and you must comply with
Occupational Safety and Health rules, wear appropriate
protective equipment.
3) The team attention
To
prevent the occurrence of harmful gas poisoning and suffocation.
must comply with Occupational Safety and Health Act and its
implementing regulations on dust against the rules, installation
of local exhaust devices or use of the effective use of
respiratory protection equipment.
Prevent
the occurrence of similar accidents and fires burning machines
1) To prevent overheating and fire caused by burning machines
I
should be grateful if you would keep
above 20cm away from the
walls and welding,
and can burn items maintain a distance of more than 50cm.
2) To prevent a fire caused by sparks and burning machines
Avoid
make sparks (Splash, Flash) splashed onto flammable materials,
or from the suction mouth parts into the open mouth internal.
3) To prevent and machinery to repair damage caused by fall
F
welder in the platform installation, to ensure security and
prevent welder slide. Requests for a fixed anchor bolt (make
sure to prevent the cylinder to fall over).
3. The venues and the installation of power equipment
1)
Installation sites
A
Direct
sunshine should be given to avoid, rain, moisture, dust small
rooms at room temperature (-10¡æ)
B
Welding
metallic foreign bodies should not have access to internal
C
Welding
20cm
from
the wall above;
And the two should be separated by more
than 30cm
up
D
In the absence of the wind arc (using wind boards)
2)
Power Equipment
Power
|
Three-phase
AC
(380V) 50Hz
|
Equipment
capacity
|
Power
application
|
10KVA
|
20KVA
|
40KVA
|
Generator
|
7.6KVA
2 times
|
18.1KVA
2 times
|
31.9KVA
2 times
|
Import
protection equipment
|
Fuse
|
10A
|
20A
|
40A
|
No
fuse breaker (Or leakage protection)
|
20A
|
30A
|
50A
|
Cable
cross-sectional area
|
Welding
power input
|
5mm2above
|
8mm2
above
|
12mm2
above
|
Welding
Power Output
|
35mm2
|
50mm2
|
70mm2
|
Ground
|
10mm2
above
|
10mm2
above
|
10mm2above
|
When
workplace relatively humid, and the monolithic, formwork on the
operation, the installation of leakage protection devices.
Attention
To
prevent damage to components, the arc of instability, causing
damage to machinery, to comply with the following requirements :
the proper use of welding
1) Allow supply voltage fluctuations is rated input voltage
range of ¡À 10%.
2)
The use of generators at the rated input
: Please use welding (7.6KVA
is 200R, 350R is
18.1KVA.
500R is 31.9KVA, 630R is
45KVA)
more
than two
times
the generating capacity of the coil with compensation.
3)
Input wiring : each equipped with the capacity required for the
automatic welding power switch circuit breaker or fuse (or
leakage protection).
4)
Please use except in accordance with no fuse breaker (or leakage
protection). For
example : the use of welding, or motor, or Transformers.
5)
Make sure the machine wire device with the designated use of
matching.
The
main welding torch welding power source and wire feeder and
composed.
First. Information technology
Technical
parameters
|
NBC-200R
|
NBC-250R
|
NBC-350R
|
NBC-500R
|
NBC-630R
|
Input
power V
|
Three-phase 380
/
50Hz
|
Samoan
import
capacity KVA
|
9.8
|
11.8
|
19.3
|
39.4
|
45
|
Output
voltageV
|
16-25
|
16-28
|
16-32
|
16-39
|
19-55
|
Admission
arc voltage
V
|
16-25
|
¡ª¡ª
|
16-32
|
16-39
|
19-55
|
Output
currentA
|
50-200
|
40-250
|
50-350
|
100-500
|
150-630
|
Resumption
arc current A
|
50-200
|
¡ª¡ª
|
50-350
|
100-500
|
150-630
|
Duty
cycle £¥
|
60
|
Wire
type of application
|
Cored / cored
|
Apply
diameter
wire mm
|
0.8£¯1.0£¯1.2
|
0.8£¯1.0£¯1.2
|
0.8£¯1.0£¯1.2
|
1.0£¯1.2£¯1.6
|
1.2£¯1.6£¯2.0
|
dimension
mm
|
710¡Á360¡Á690
|
680¡Á360¡Á700
|
675¡Á375¡Á755
|
675¡Á435¡Á765
|
850¡Á470¡Á820
|
weight
kg
|
110
|
101
|
131
|
178
|
250
|
Model
|
NBC-160
|
NBC-200
|
NBC-250
|
NBC-500
|
Power
Voltage (V)
|
380
|
Power
Phase
|
3 |
Currency
Regulation Range (A)
|
¡¡30-160
|
40-200
|
60-250
|
80-500
|
Continuous
Loading Rate (%)
|
60 |
Specified
Capacity (KVA)
|
¡¡4.8
|
6.0
|
9.5
|
22
|
Welding
Thickness (mm)
|
¡¡0.6-3
|
0.8-6
|
0.8-8
|
1.1-14
|
Quality
(kg)
|
¡¡105
|
120
|
140
|
245
|
Second.
Structure
1¡¢Part of three-phase power transformer, rectifier, reactor,
the control circuit and chassis outwardly composed.
2¡¢Wire :
The
main structure of a wire device wire (which includes motors,
gear box, round wire-school straight round clamping device, wire
joints), rack, solenoid valve, silk Shaft, plug and socket
components, trachea components, control boxes and other
components. Interface
type remote control boxes and gun users need to be equipped
with.
Third.
Use and maintenance
1¡¢Welder
should be installed at ambient temperature does not exceed 40 ¡ã
C and relative humidity below 90% (25¡ãC), non-corrosive
gases. water, steam, chemical deposition of dust particles, mold
and other explosive local media. Meanwhile welder should not be
a serious vibration and impact.
2¡¢Do
not have the time or the installation of new welder, the welder
must be examined prior to the use of not less than 5 megohm
insulation resistance. output side of the insulation resistance
to not less than 2 Megohm.
(Note : check should first output
terminal wiring short), if they are less than the above value,
the first welder for use in drying.
3¡¢The
installation :
(1)
Welder be reliable grounding :
(2)
Circuit and gas link :
Input
terminal wiring welding, pipe welder at the joints after the
panel, preheater power output socket wiring at the front end
plate. gun control cables and sockets in welding joints trachea
out front.
Priorities
: connecting gas cylinders - preheater-valve-welding-torch.
Weld
received a three-phase circuit connecting sequence :
(380V,50Hz power, gun control to the cable socket. will torch, welding
cable welder output "+" very, welding cable to the
workpiece welder output "-" very, will preheater
preheater electric welder received on the socket.
4¡¢After
the link above, welder to be energized.
Opened
at the front plate welding control "power" switch, the
light is bright.
And
round wire to wire through the welding torch, tip and check the
wire operation, blocking phenomenon.
Preheater
and the switching valve open, open, "Frederick gas"
switch, check and adjust the gas flow protection. After the
closure, "Frederick gas," Switch.
Upon
completion of these preparations, both for welding torch at the
buttons, can be pressed for welding, loose welding stop.
Welding
adjusted by the panel at wire speed knob on the voltage
regulator pronounced complete.
Inductance different welding
requirements of the regulation that is needed? Different sizes
of the wiring current output.
(1)
Power conditioning; Voltage Regulator step one. Rough adjustment
switch three ratings : rough adjustment, multiple voltage
regulation increased.
2. Switch : fine-tune fine-tune the
sub-10 stalls, conditioned on the base coarse adjustment knob
adjustments to fine-tune the voltage switches will Incremental.
(2)
Wire speed adjustment :
Current
regulation wire feed rate is adjusted according to the welding
process, welding technology, adjustment knob to achieve the
optimum wire feed rate front plate welding current.
(3)
Inductance options :
The
welder use multiport anode output, the output terminal
inductance, in order to facilitate the users choice.
5¡¢Maintained
:
(1)
The corresponding rate of sustained load using welding.
(2)
Observe the tip wear, such as severe wear badly in need of
replacement.
(3)
Periodic inspection of wire, wire round of severe wear it.
(4)
Do not repair the torch, torch will be prohibited after work on
the platform. Forced myself not to put links welding,
and not pressure drop.
(5)
Welder to keep clean.
Fourth.
Troubleshooting
Fault
|
Reasons
|
Exclusion
|
Low-load
voltage
|
1¡¢Single phase operation
2¡¢The input voltage is not correct
3¡¢Three-phase full-wave rectifier for the group,
a silicon component damage (short or way)
|
1¡¢To check the labor costs of insurance, such as
burn-please replacement.
2¡¢Input supply voltage checks, and transferred
rating.
3¡¢Rectifier diodes check whether there are short
- or way phenomenon.
|
No-load voltage regulation and the scope of the
normal
|
1¡¢KHS Universal Contacts have access switch.
2¡¢Coil tap lead levels out of a transformer
fault.
|
1¡¢Check for the presence of the Contact Xu Han,
then check for the presence of false leads, should be
replaced if damaged switch.
2¡¢To check if the stall than normal voltage
transformer coil or repair Lead.
|
Wire
is not functioning
|
1¡¢The control circuit or fuse wire circuit Burn.
2¡¢The wire-speed potentiometer zero.
3¡¢AC contactor not move.
4 ¡¢Wire circuit malfunction, adjusting
transistor preservatives, W1 and the potential for damage
to degenerate LM317 other components.
5¡¢The electrical fault.
|
1¡¢The replacement of fuse.
2¡¢The wire feed rate adjustment knob.
3¡¢It moves inspection of printed circuit boards
DC relays, circuit if lost, Contact DC Relay check whether
good contact, such as damage to be replaced.
4¡¢As detailed brochure control circuit, the
replacement of defective parts.
5¡¢Electrical repairs.
|
CO2
shielding gas is not cut out or not
|
1¡¢The electromagnetic valve malfunction.
2¡¢The flow device nowhere.
|
1¡¢Check loop electromagnetic valve, the valve
ends 36V AC voltage, the valve is damaged, repaired or
replaced.
2¡¢Overhaul CO2 gas heating, vacuum flow device.
|
Uneven
transmission wire welding process
|
1¡¢Wire roller wear.
2¡¢Pressure wire handle pressure enough.
|
1¡¢The replacement of wire roller
2¡¢Spring increased the pressure on the handle or
the handle with a downward displacement blocks after the
bear.
|
Weld
porosity
|
1¡¢CO2 gas or impure water containing too many.
2¡¢Or abnormal flying nozzle was blocked.
3¡¢Current, voltage, welding speed is too large,
too small gas flow.
4¡¢Wire Deoxidizer contained too little.
5¡¢Convection of air around too much.
6¡¢Welding pieces of dirty or wet.
|
1¡¢CO2 gas purification.
2¡¢Adjusting or cleaning.
3¡¢Adjusted norms, adjusted for flow.
4¡¢For wire.
5¡¢Defensive style device.
6¡¢Clean weldment.
|
The
process of welding spatter excessive
|
1¡¢The anti-Connected
2¡¢Regulate improper "such as high voltage
and current".
3¡¢The wire feed rate instability.
4¡¢The wire stretched out too long.
5¡¢Tip wear.
|
1¡¢Anode should access the workpiece.
2¡¢Adjusted norms.
3¡¢The control circuit inspection, electrical,
wire wheel and pressure handle with silk spring compress
degree.
4¡¢And cut the distance between nozzle and
welding pieces of the "short circuit welding when >10mm
5¡¢The replacement tip.
|
Workpiece
welding cracks
|
1¡¢The workpiece is dirty;
2¡¢The high wire sulfur, manganese low;
3¡¢Welding unreasonable.
|
1¡¢Cleaners;
2¡¢Wire transfer;
3¡¢Changing process conditions.
|
Weld
Depression "occlusion"
|
1¡¢High-speed welding;
2¡¢Far below current welding speed;
3¡¢Torch angle too.
|
1¡¢Lower welding;
2¡¢Adjusted norms.
3¡¢Correct perspective.
|
Rong
deep enough
|
1¡¢The current low;
2¡¢Low voltage;
3¡¢The length of wire stretched out too much;
4¡¢Then anti-polarity;
5¡¢Fine wire, workpiece thickness;
6¡¢Welding pieces groove is too narrow, too small
angle, the gap is too small.
|
1¡¢Increasing wire speed;
2¡¢Adjustment switch position;
3¡¢Reducing the extended length;
4¡¢Correction
5¡¢Corrections
|
Weld
irregular in shape
|
1¡¢The wire stretched out too long;
2¡¢The
wire
too hard;
3¡¢The current relatively high voltage;
4¡¢Welding speed is too low;
5¡¢Wire-speed instability.
|
1¡¢Reducing the extended length;
2¡¢Wire transfer;
3¡¢Lower wire feed rate;
4¡¢Higher welding speed;
5¡¢The inspection control circuit, the electrical
wire wheel and pressure handle with silk spring compress
degree.
|
Did not send wire
|
1¡¢The pressure did not
play a role round
2¡¢The electrical
switch is not
|
1¡¢The pressure to wire
2¡¢The electrical cable
joints whether the relaxation should be replaced if the
electrical fault
|
Courtesy of instability
wire
|
1¡¢Round wire in the
wire between Ferry and sliding pressure
2¡¢Wire and wire
diameter sizes inconsistent round of trench
3¡¢Excessive bending
gun hose
4¡¢The guide wire into
the dirt tube
5¡¢The inner surface
conductivity mouth too rough
|
1¡¢Adjust pressure
2¡¢Round wire-transfer
surface or replacement
3¡¢Will directly reduce
the whole bending Bend
4¡¢The clean-up or
replace wire
5¡¢The replacement
torch tip
|
Protection not send gas
|
1¡¢Did not open the
main valve
2¡¢The high pressure
3¡¢Solenoid valve
malfunction
|
1¡¢Opened the valve
2¡¢Regulate pressure in
the following 5kg/ cm2
3¡¢Remove or replace
the solenoid valve failure
|
Wire bending donated
|
1¡¢The school has not
tuned in straight round
2¡¢Bending gun catheter
serious
|
1¡¢School adjustment
straight round
2¡¢Reducing the
curvature
|
|